How I Use 3D Printing in My Leather Workshop
When I first got into leathercraft, the idea of using a 3D printer felt like it belonged to another world — maybe woodworking or electronics, but not a leather bench. I was wrong. A year into owning an Ender 3 and integrating it into my workshop, I now consider it one of the most unexpectedly useful tools I’ve added to my kit.
Initially, my goal was simple: make custom stitching jigs. I was tired of trying to hand-align stitch lines on curved pieces or repeat the same spacing on a dozen belts. I designed a simple stitch guide in Fusion 360, printed it in PLA, and within a few hours I had a perfectly usable tool. That first test was rough — the layers were uneven, the plastic warped slightly — but it worked. And it showed me what was possible.
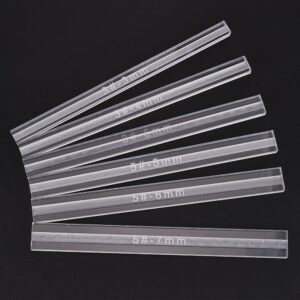
Since then, I’ve printed jigs, corner radius templates, edge creasers, and even full wet-forming molds. One of my favorite prints is a snap-setting base with different insert slots. It’s saved me from misaligning hardware more than once. I’ve experimented with PETG and carbon fiber blends, too — the durability is noticeably better for high-stress parts, though they take longer to dial in.
Not everything was smooth. My first mold for wet forming collapsed after just two uses — printed too thin, in the wrong orientation, and with the wrong filament. I’ve learned to print molds in thicker walls and denser infill, sometimes using supports and sometimes splitting molds into multiple parts and screwing them together. It’s a learning curve, but worth every misstep.
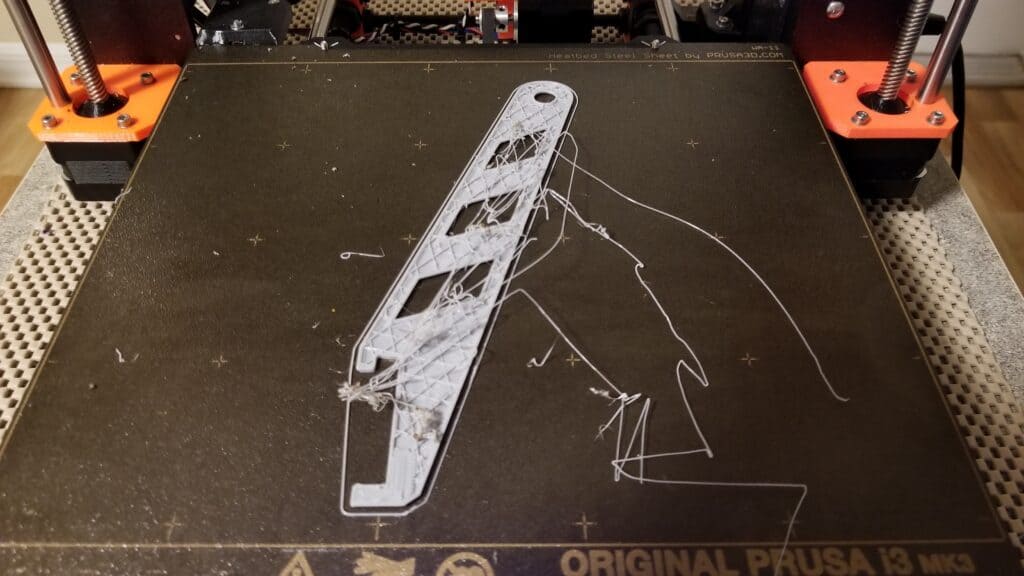
The biggest win, though, has been brand customization. I printed a logo stamp using a high-resolution nozzle and TPU filament, then used it for cold stamping on veg-tan leather. It’s not a substitute for a brass stamp, but for small batch runs and prototypes? It does the job surprisingly well.
One thing I didn’t expect: how 3D printing has changed the way I think about workflow. Now, instead of adapting my project to the tools I have, I make the tools I need. That’s a powerful shift. It’s made my shop more efficient, and honestly, more fun.
If you’re already comfortable with basic leatherwork and like the idea of blending tech with tradition, a 3D printer — even an entry-level one — might surprise you. It won’t replace your awl or your knife, but it might just become your secret weapon for solving those annoying, repetitive workshop challenges.